Parts and Tools
Here's the parts you'll need to make one pocket-sized drunken robot. But make more than one since it's no fun to drink alone.
Parts
1 vibrator motor from a pager or cell phone. (I used these. You can find the same motor here and here, though it seems distributors keep selling out. Just about any tube-shaped vibration motor with two metal tabs on the end will work. Search for more.)
1 AG13 button cell battery. A common watch battery that also goes by the aliases 357A, L1154, LR44, GPA76 or PX76A.
1 square inch of sheet tin, copper or other easy to work with metal sheeting. You can probably use a tin can but it might be hard to work with. I'll be using 0.008" sheet tin from the local hobby store.
The PDF template linked below.
Tools
Pliers
Tin snips. (or old crafty scissors you don't mind messing up to cut some tin.)
Now that you have everything, lets get started!
CUT THE TIN:
Print out the template from step 1 (also linked below) Be sure to print it at 100% and transfer the design to your piece of tin. (Cut it out and trace it or just glue it on with some temporary adhesive.)
Cut and snip your tin on the solid lines. Please be careful when cutting and handling sheet metal since it can get really sharp. Gloves and safety goggles are recommended.
NOTE THAT THE NEGATIVE SIDE OF THE BATTERY IS ON TOP
Make The Holder For The Battery:
We want to make a solid connection to the side and bottom of the battery. To do that first bend the piece of tin up at right angles where it's indicated on the diagram. Then place the battery in the middle and fold the arms around so it holds it securely.
Prepare The Motor:
Our pager motor has two leads. One needs to be connected to each side of the battery for the motor to work.
The flat side of the battery (+) is already making contact with our tin support. To get a contact with the top of the battery (-) we bend one of the pins back underneath the motor. When we put the motor in place this lead will spring in contact with the top of the watch battery. (Picture is worth a few hundred words here.)
If you're using a different motor, say one with wires then you might need to get busy with a soldering iron to replicate what we have here. Do not solder directly to the battery. Applying that much heat to a battery is dangerous and can cause it to burst.
BEND ONE OF THE LEADS OF THE BATTERY AS SHOWN
Mount The Motor:
Now we're going to complete the circuit by crimping the motor (lightly!) into the top pair of tabs. This will press the bent tab in contact with the top of the battery and the lead into contact with the tin which will complete our circuit.
First bend the top tabs of our tin into a U shape so we can rough everything into place. Then place the motor so that the bottom lead is in firm contact with the battery while the other lead is pressed against the metal of our tabs.
(You might want to put a piece of paper or tape over the top of the battery to keep our robot quiet while we're working on him.)
Very carefully crimp this closed with pliers. You want the motor to stay in place, but you don't want to damage the casing of the motor.
.jpg)
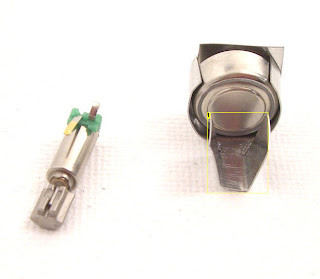.jpg)
.jpg)
.jpg)
Troubleshooting:
It doesn't go at all.
First be sure that the motor leads are touching the things they need to touch, and only those things. One should be touching the top of the battery and the other should be firmly pressed against our tin framework.
Check for shorts. Make sure that the only bit of metal touching the top of the battery is
Make sure that there is nothing keeping the weight at the top from spinning.
It falls over more than I'd like.
There are several ways you can counteract this.
Bend the motor back towards the center of the battery so its center of gravity is more in the middle.
Bend down the corners of the "front" of bottom platform.
It might be too vigorous, you can try letting the battery run down a bit so it doesn't jump as much.
Try a different surface. I found that a pad of paper was the most reliable. On a harder surface they'll bounce easier.
Get out a file and remove some of the weight from the top of the motor.
It falls over less than I'd like or doesn't act very drunkenly.
Give it a double whiskey neat and wait 10 minutes.
You might be using an under powered battery., especially if you're using a bigger motor. Try a fresh battery or a more powerful cell. (If you use a different battery you'll need to rework the tin holder.
Make sure the motor isn't shaking lose. If it is, a dab of glue or tape can take care of your troubles.
DOWNLOADS: